The history of customization is as ancient as the history of design. And there are three principles that have governed the need for customization – form, fit and function. Intimately intertwined with this quest for customization is the history of material development – mud, stone, wood, concrete, steel, superalloys, composite materials, ceramics, and so on. Keeping pace with these new materials has been the maturation of their manufacturing processes – for metals these include casting, forging, molding and now Additive Manufacturing (AM), which is the focus of this blog series.
Simply put, AM is an umbrella term that describes a “layer-by-layer” deposition process used to build an item, typically accomplished by a 3D Printing machine and a CAD model of the item. Depending on the industry and the raw materials used, the processing methods have specific nomenclature. For metals, Direct Metal Laser Sintering (DMLS) – and closely-related processes Selective Laser Sintering (SLS) and Selective Laser Melting (SLM) – have gained popularity since the mid-1990s, becoming particularly more sophisticated in this decade. Techniques such as these hold the promise of revolutionizing current paradigms in engineering design, manufacturing, and performance. Imagine: building components that are lighter-weight (form), geometrically-complex (fit), and structurally-equivalent/superior (function), all at a faster pace and with a smaller factory footprint. The Holy Grail is within our grasp, right? Well…not so fast.
To fully realize the potential of AM, significant advances are needed in both the process and performance modeling of additively manufactured materials and structures. The simulation of AM from “cradle to grave” is multidisciplinary in nature, involving multiple physics as well as multiple time and space scales. Interdisciplinary research efforts are therefore required in order to fully understand how everything fits together. Fortunately, the digital architecture of AM affords the possibility of efficiently integrating computational modeling with real-time measurements taken during the build process itself.
While AM as a technique might be new, it is being applied to traditional alloy chemistries. If you take the same alloy and run it through a selection of conventional processes (such as casting, forging, welding, heat treating), each path will give you a different microstructure. This, in turn, drives different performance properties (static strength, fatigue strength, etc.). The AM process creates its own signature in the material; any combination of changes in machine settings (laser power, scan speed, hatch spacing, layer thickness, etc.) will influence the resulting microstructure. Regardless of the manufacturing method, the mandate to produce a robust product with high reliability remains the same. And some of the unique challenges of AM, like finding those optimal machine settings, underscore the need for effective modeling of microstructural variability.
The physics-based probabilistic tools in VEXTEC’s VPS-MICRO® software, which are successfully predicting durability of conventionally-manufactured products, is being adapted at the microstructural level to meet AM head-on. In the second part of our blog series, we’ll show you how VEXTEC’s technology is being used in the cutting-edge world of additive manufacturing.
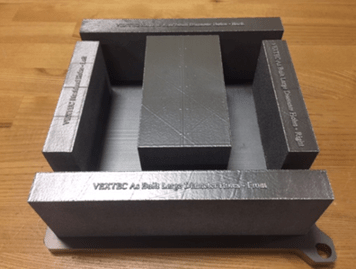
Ti-6Al-4V alloy blocks built by AM. Photo courtesy of the Manufacturing Demonstration Facility (MDF) at Oak Ridge National Laboratory (ORNL).
Leave A Comment