Earlier this year, the Air Force Research Laboratory (AFRL) launched its QUalificaiton of Additive Structures for Aerospace Requirements (QUASAR) Program. The intent of this program is twofold: to identify state of the art and current gaps in the qualification and certification (Q&C) activities for additively manufactured (AM) fracture-critical metallic parts; and to mature technologies that can close the gaps. Government and industry stakeholders have since begun working together to identify those deficiencies, chief among them being the current physical testing burden involved in Q&C. This required level of testing has direct impacts on both the schedule and cost of AM part availability, which in turn can affect warfighter readiness.
AFRL and its primary collaborators (ARCTOS, The Barnes Global Advisors) have identified the main challenges in Q&C being:
- effective/efficient non-destructive inspection techniques;
- how to handle as-printed surfaces and articulate their debit to performance; and
- lack of harmony in current Q&C approaches (multiple standards including AWS D20.1, NASA-STD-6033, AMS 7032, AMS 7003, EZ-SB-19-01).
The group has determined that adopting validated defect- and microstructure-inclusive modeling is the path forward to reduce the testing burden. They will explore the benefits of available modeling tools by comparing a “full testing” example to a “reduced testing” example that includes modeling, and demonstrating equivalent confidence between the two approaches. The proposed “reduced testing” example would take advantage of specimen-level testing (which is less expensive and time-consuming) to collect microstructure and defect data to inform the models. These models would then be used to predict equivalent initial damage size (EIDS) distributions and performance for a fully sized and geometrically complex part. Limited physical testing of parts would be used to validate the model-assisted analyses.
VEXTEC’s approach of model-assisted AM qualification aligns seamlessly with AFRL’s objective. Our VPS-MICRO® Software integrates materials science principles with standard structural engineering tools such as finite element analysis to model fatigue performance at the microstructural level, where damage actually occurs. Our tool has been used by both the Department of Defense as well as the private sector to predict the risk of cyclic fatigue failure of AM parts based on location-specific microstructure, defects, residual stress and surface roughness. Last month, VEXTEC was invited to participate in a QUASAR Program Update at AFRL offices in Dayton, Ohio. VEXTEC’s digital tools were highlighted as a means to integrate AM as-printed surface features.
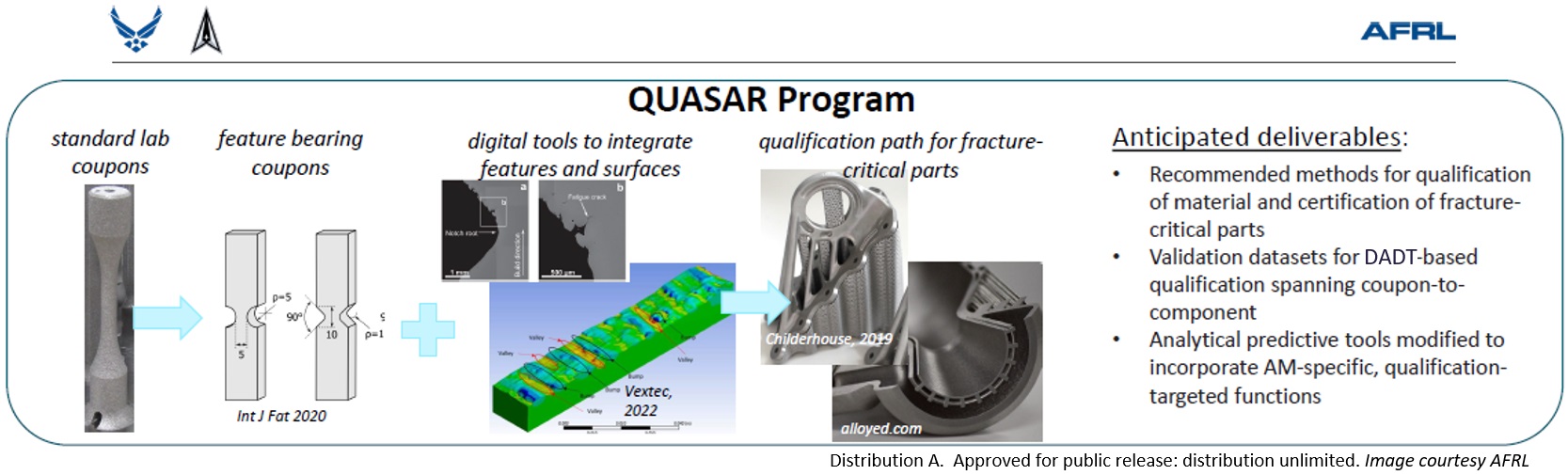
AFRL QUASAR Program
VEXTEC looks forward to continuing our long-standing collaboration efforts with AFRL, and advocating for materials-based computational tools that lower barriers to AM adoption in the aerospace industry.
Leave A Comment